Color management is a process practiced by graphic arts professionals who need to ensure that the colors produced on their printers and other imaging devices will reproduce accurately and consistently. Within graphic arts there are a number of environments in which color management is usually considered critical some of which include the pre-press and proofing department of a professional printing operation, high-end photography and fine art reproductions.

In these types of graphic arts environments where color management is critical, ensuring that all output devices and printers are accurately reproducing color helps keep the operation’s workflow moving and minimizes wasted time and material.
In this article we’ll take a look at the components of color management, describe how a spectrophotometer is used to measure color output and discuss several factors to consider when implementing an advanced color management solution.
It’s important to note that unlike most office and home printing environments – where colors are usually measured subjectively on the basis of whether or not it matches what was expected (i.e. does it look right?) — color critical environments require a more reliable method by which to achieve precise color reproductions. Typically, it’s a level of color precision that is specified relative to an industry-standard set of color values. We’ll call this objective color accuracy because the output can be measured and compared to a desired, numerical outcome.
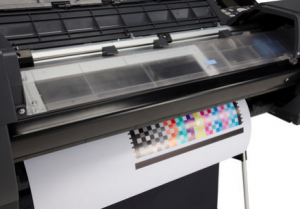
Achieving objective color accuracy therefore requires that output devices and printers be calibrated to a known reference point; such as the device’s original factory settings or, alternatively, to a standard color space such as L*a*b for RGB, or Gracol for CMYK. In environments in which multiple devices are used, keeping all printers calibrated to the same standard ensures both color accuracy and consistency, thereby enabling any device or printer to be selected for any job.
Among the specialized tools used by these professionals to implement an effective and objective color management process is a device called a spectrophotometer which is used to measure color values. In addition to the spectrophotometer the color management process also requires a reference color data set and software for analyzing the measurement data and generating profiles for an output device – such as a printer.
A spectrophotometer is a color measurement tool used by graphic arts professionals who require a high level of color accuracy and consistency. A spectrophotometer uses a fixed light source and sensor to measure the amount of light that is reflected by the inks and media surface. To maintain the highest level of accuracy, the light source’s wavelength is set to a known reference point and then a standard color, such as white, is first scanned to calibrate the sensor.

A spectrophotometer is able to measure light across the entire visible spectrum and capture the complete range of spectral and reflective characteristics for each color on a printed reference chart (aka patches). This capability makes it the ideal tool for gathering the data needed in color-critical environments where objective color accuracy is required.
Color management in a graphic arts environment is accomplished via a profiling process whereby each type of print media used in the operation is imaged with a reference chart of color patches and then scanned by a spectrophotometer to measure the color values that result. These color values can then be used to make the adjustments needed to achieve the desired state of accurate and consistent color reproduction.
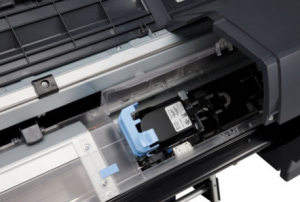
When the spectrophotometer’s scan operation is completed, specialized software then analyzes the data and compares the results to a set of standard values. The variance between the measured and standard values can then be used to generate a target profile for each device and media type used in the operation. In addition to the variance values, the profile-generation software also takes into account the physical characteristics of the media as well as the color gamut of the inks.
How and where the resulting profiles are installed will vary depending on the particular types of devices and printers used in a given environment. For example, in operations where printers from the Canon iPFx400 large-format series are used, profiles are loaded directly into the printer’s controller. This capability makes profiles immediately available to all users. In other cases, profiles may need to be copied to the printer driver on each work station, which may lead to synchronization problems. And in operations where a RIP is used for color and print management, the profiles are typically automatically installed into the RIP database. Regardless of how the profile is installed, however, it will accurately reproduce colors only on printers that are properly calibrated.
Spectrophotometers offer the most value when utilized as part of an advanced color management solution. Such solutions take different forms.
- Color management software uses spectrophotometer data for calibrating printers and generating media profiles. These tools typically support ICC as well as printer manufacturer profile formats. Color editing features allow users to make adjustments to individual colors.
- RIP solutions often integrate advanced color management capabilities with their other functions. Unlike color management software, a RIP bypasses the printer driver and accesses the printer directly. This enables the RIP to generate profiles in a proprietary format and allows for more detailed color information than is available using industry-standard formats. A unique feature of one RIP, the OverDrive RIP from ColorBurst, is designed to utilize the RIPs color management features for ICC profiles, but uses the manufacturer’s driver for data output. (this is the only RIP that uses a combo of RIP color management and the Canon driver.)
- Printer manufacturers, like Canon, offer models with an integrated spectrophotometer and provide software that uses those measurements to generate media profiles. Similar to a RIP, manufacturer profiles typically contain more color and rendering information than an industry-standard profile.
The spectrophotometer units themselves are designed in a variety of shapes and sizes. Standalone desktop and handheld devices are the most common. Some read a single line at a time while others auto-scan an entire page. As an alternative to a handheld spectrophotometer, Canon offers an optional onboard SU-21 Spectrophotometer that attaches to the 24-inch wide imagePROGRAF iPF6450 large-format printer.
The SU-21 Spectrophotometer can be used as the basis for color management across an entire fleet of iPFx400 series of large-format printers. The SU-21 Spectrophotometer can also be used to manage internally created media profiles and allow the profiles to be shared across a network with other iPFx400-series printers.
While it is important to weigh the general capabilities of a color management solution and spectrophotometer, there are also some not-so-obvious features to consider.
- Precision is a key factor in choosing a spectrophotometer. Measured on a ∆E color-difference scale, precision reflects variances in repeated measurements of the same color. The lower the ∆E value, the better. A disadvantage of using a handheld spectrophotometer is that the manual positioning of the device can adversely affect precision if the distance between the device and the media varies while scanning.
- XGRA is a standard introduced in 2010 by X-Rite for mapping spectrophotometer measurements to color values. By selecting a spectrophotometer that conforms to this standard, users can be certain that the measurements used for profiling purposes will avoid the types of mismatches that can occur with an older or non XRGA compliant spectrophotometer.
- Some spectrophotometer profiling operations take several hours to complete, particularly if the process requires manual scanning and data entry. By automating the entire process – patch printing, drying, scanning, analysis and profile generation – and then optimizing each step, a solution can significantly lower profiling times and raise accuracy levels.
- Color management in multi-printer environments poses a special challenge, particularly if printers are in different locations. Look for a solution that centralizes advanced color management and automatically shares a single profile among all printers of the same class.
- The ability to print on a wide choice of media types is important for operations that offer specialized creative services. Features that impact color accuracy on custom media include varying the spectrophotometer’s height to accommodate media thickness and the ability to turn the UV-blocking filter on and off. Typically, UV light is allowed to pass to the sensors in order to eliminate the effect of whitening agents in some papers. Filtering is turned on for profiling papers that do not have whitening agents. Many solutions do not allow users to alter the UV setting, thereby restricting media choices.
- Printing operations that use a RIP for color management or proofing will benefit from a profiling solution that integrates with the existing workflow and toolset. Consider a solution that is fully integrated into the RIP’s advanced color management function. Specifically, the solution should allow the RIP control of the patch drying and scanning process, access to the measurement data and the capability to generate equivalent standard profiles for use on printers not controlled by the RIP.
- Color-critical applications demand not only objective color accuracy, but also the highest level of consistency attainable. In large multi-printer environments, consistency among the entire fleet of printers is as important as it is for a single printer. Fleet-wide consistency starts by calibrating all printers to the same baseline. Other factors include sharing of profiles for new media and automatic compensation for calibration differences among printers.
The color management process utilizes color measurement data collected by a spectrophotometer and specialized software to control image quality in applications where objective color accuracy is required.
Proofing, fine art reproduction, commercial photography and corporate branding applications can all benefit from this type of advanced color management. In addition color management solutions can also be used to support custom media and fine-tune media profiles.
There are several factors to consider when choosing a color management solution and spectrophotometer. Among them are the precison and standards compliance of the spectrophotometer, automated versus manual profiling operation, profile sharing among printers, support for a wide range of media types, integration with existing RIP workflow, and support for fleet-wide accuracy and consistency.
Click here to learn more about Canon Wide Format and Color Management